FAQ’s
Do I need a cosmetic safety report?
By law, you must have a safety report before you can sell a cosmetic product in the EU or the UK. This applies if you have created your own recipe, or if you have used a recipe you’ve purchased from a wholesaler.
What counts as a cosmetic product?
In simple terms, anything that is intended to be put on the hair, skin, nails, lips, teeth, or gums to improve or change their appearance or smell is considered a cosmetic product. If you are unsure whether your product would be considered as a cosmetic, email me and I’ll let you know.
Are your reports expensive?
The amount I charge depends on how many ingredients you have used in your product recipe. On average, my clients pay £250 for their first report, but it could be more or less, depending on your recipe. Generally speaking, my reports are not the cheapest, but they are the most thorough and give you everything you need to comply with the regulations in the UK and all EU countries.
Are all cosmetic product safety reports the same?
In short, no. All safety assessors have their own way of doing things, and use their own templates for the reports. Some assessors may offer different options, such as a very low cost option for a shorter report that is missing some information needed to comply with regulations in certain EU countries. Before you pay for a report, it is important to check that the assessor will provide everything you need to comply with the regulations of the country you are selling your product in.
The reports I provide are extremely thorough, and contain everything you need to sell your product in the UK and all EU countries.
Will I need to send you a sample of my product?
No. I’ll ask you to fill in a form that tells me what’s in your product, and how much of each ingredient there is. I’ll use this information to assess whether your product is safe and compliant with the rules in the UK and EU.
Is the form complicated to fill in?
You’ll need to provide a lot of information on your forms, and some of it may seem like scientific jargon. To make the process feel less overwhelming, my forms have links to videos showing you how to fill them in, and explaining any jargon in everyday terms. If anything is unclear, you can arrange a call and we’ll chat it through together.
What if my recipe isn’t safe or compliant, and I need to change it?
If I can tell your recipe will need adjusting from the information you provide in your quote request forms, I’ll let you know and tell you how to fix it before we move forwards with your report. If I discover that your recipe needs to be changed during the assessment, I’ll let you know and tell you how to fix it. Once you’ve adjusted your recipe, I’ll revisit your report for no extra charge.
Will I understand the CPSR?
I do all the hard work of looking at the safety regulations so you don’t have to. If you have any questions once you have the report, email me and I’ll happily talk it through with you.
Will I need to get other compliance checks or tests done before I can sell my product?
Depending on your product, some extra tests and checks may be needed before you can start selling it. If you are unsure about which checks you need, I’ll give you guidance and refer you to businesses that provide these services. I’ll only refer you to testing companies that I know and trust. Also read my blog on what to do before requesting a CPSR.
What do I need to be able to sell my cosmetic product legally in the EU/UK?
The minimum requirements for selling a product are:
1. Product Information File (PIF) held in the EU and / or UK. For information about the content of the PIF see Cosmetics Europe (search for PIF). There is no central database for this, but a copy needs to be retained at an address in the EU and / or UK which is included on the label.
2. CPSR (Cosmetic Product Safety Report ie. safety assessment report)
3. Notify the EU CPNP portal and / or the UK SCPN service (UK Guidance for SCPN; user manual for EU CPNP and instruction video for CPNP)
4. Correct labelling of the product (labelling guidance from Cosmetics Europe)
What is a PIF?
What is an INCI name?
INCI stands for International Nomenclature of Cosmetic Ingredients. It is used for product labelling for the ingredient list (see http://www.personalcarecouncil.org/science-safety/inci for further information).
If the ingredient in a product has an INCI name available, it should be used. If the ingredient does not have an INCI name, other rules apply (please contact us if this is relevant to your product). Official INCI names are listed in the EU glossary at https://eur-lex.europa.eu/legal-content/EN/TXT/?uri=CELEX:32019D0701 but a more user-friendly searchable resource is here: http://ec.europa.eu/growth/tools-databases/cosing/, and also indicates if the ingredient has any restrictions, but note that this database is not the official, legal source of this information – for that you should refer to the actual legislation https://eur-lex.europa.eu/LexUriServ/LexUriServ.do?uri=OJ:L:2009:342:0059:0209:en:PDF.
What is a challenge test / preservative efficacy test (PET)?
A microbial challenge test (also known as PET – preservative efficacy test) is a specialised test where the final product is ‘challenged’ with bacteria, mould and yeast, (they are deliberately added to a sample of your product) and left for 28 days to see if anything grows.
If too many bugs grow, your preservative is not suitable for the final product, and the recipe needs to be amended. A new challenge test will be required. It is also a good idea to conduct a challenge test on an aged sample.
Generally a challenge test is required when you have water in your product (there are exceptions, please contact us if you are unsure).
The following UK-based company carries out challenge tests:
What kind of stability testing do I need?
Stability observations are observations of your product’s performance over time (e.g. appearance, colour, odour, pH).
The observations should be recorded and saved in a report, which is stored in your PIF and a consideration of the stability of the product is required in the CSPR.
Do you have any older batches that have been stored / kept? For non-water containing products, for the purposes for the safety assessment, I can accept 1 month at room temperature, generally. But you should continue the observations yourself and record them in the PIF to support the shelf life of the product.
When you do stability testing, try to do it in the final packaging so that you also get information on the packaging compatibility of the product and the pack you have chosen.
Keep some samples from each batch you make, to monitor how they perform at room temperature. After a certain time period, make a note of the appearance, odour and colour and changes (if any), and this will provide evidence to support the shelf-life.
If your product contains water e.g. an oil in water emulsion, one way to check that the emulsion is stable is to store it at elevated temperatures (greater than 35°C) for 3 months which will give an indication of what might happen in the future, when your product might be stored for long-term at room temperature. The ability to store samples at higher temperatures is very difficult to achieve at home and therefore a specialist laboratory can be useful. If you get satisfactory stability results after 3 months you can confidently put a shelf-life of at least 12 months (and many companies use 24 months) on your product.
The following UK-based companies carry out stability tests (and may also do other analytical testing and services such as claims substantiation / user trials etc):
Emsworth emsworthstabilityplus.co.uk/
Sensory Dimensions sensorydimensions.com
Source Bioscience sourcebioscience.com
Marfleet Analytical marfleetanalytical.com
If your product does not contain water: only minimal stability testing is required, such as 1 month at home, in various locations. This will give you evidence to start with a shelf life of 6 months, and as you gain more data you can extend it further.
Special case – soap, dry products: Do not need any stability test in particular.
Can I use a manufactured base to make my own cosmetic products? What do I need to consider?
A number of companies make and sell a cosmetic base which brand owners can customise, in order to sell a range of products with differing scents and / or colours. A CPSR (see Get a CPSR) is required for the finished products. The supplier of the manufactured base will often provide the brand owner with the results of testing such as stability or challenge testing (where applicable), but at a minimum, needs to provide a full recipe (percentage bands are acceptable) and a list of specification tests and criteria for the base formulation.
The manufacturer may also provide manufacturing suggestions such as the maximum additions allowed, but in general an addition of up to 2% perfume / essential oil / colour is acceptable before any further testing such as stability or challenge testing (where applicable) is required. If other ingredients are added, the finished product variants will usually need further testing (stability or challenge testing (where applicable)).
Why do I have to specify a supplier of my raw materials? What if I want to change a supplier in the future?
When I review a recipe I sometimes need some clues as to exactly what the ingredient is, and the supplier’s details can help with that (eg I can look on the supplier’s website, or I might have come across the ingredient from that supplier before).
If the ingredient is a mixture the supplier needs to be listed, because different suppliers can have the same product but it be composed of different ingredients, for example ‘Calendula Oil’ from Supplier A could be 10% Calendula Officinalis Extract and 90% Helianthus Annuus Seed Oil, and from Supplier B could be 8% Calendula Officinalis Extract, 91% Helianthus Annuus Seed Oil and 1% Tocopherol. All the component ingredients need to be considered in the safety assessment, and they all need to be taken into account when generating the ingredient list.
If the ingredient has a legal purity requirement, then the exact tradename and the supplier need to be listed. For example ‘Carbomer’ has a requirement for use in cosmetics ‘not allowed if contains > 0.1% benzene’. Different grades are available for different industries and therefore I check which grade you are proposing to use.
If you want to change supplier in the future for new batches: if it isn’t a mixture, and there are no legal purity requirements, you can do a swap, but you should record this in your own documentation (e.g. PIF) to show you have considered the impact, and decided that there is no difference between the version that was safety assessed, and this new version.
If it is a mixture and/or has a legal purity requirement, the safety assessment report needs to be reviewed and probably amended / updated (which will incur a fee, but a lot less than the price of a full report).
If you know that you will use different suppliers, put them all in the submission, or ask your safety assessor to only list the supplier where it is required (ie mixture or purity requirement).
Why do I have to list the packaging of my product(s)? What if I want to change it in the future?
It is a requirement in the Regulations that the safety assessment needs to contain a consideration of the packaging, (in Annex 1 of the Regulation it states: “The relevant characteristics of packaging material, in particular purity and stability”).
If you want to change your packaging in the future you need to consider whether there will be an impact on the safety assessment. If the proposed change was e.g. from one type of glass bottle, to a differently shaped glass bottle, the impact would be negligible and you could record the change in your own documentation. If you are changing from one type of polymer / plastic to another, I would suggest you need to have a chat with your safety assessor about what might need to be done.
Why do you suggest food grade packaging?
Packaging safety evaluation has to take into account a range of directives and regulations eg 1223/2009 (cosmetics), REACH, 10/2011 (plastic materials and articles), 94/62 (packaging and packaging waste), 2011/95 (general product safety).
In 1223/2009 it states that information should be given on the packaging material, impurites and traces (Annex 1, section 4) and in the SCCS Notes of Guidance it also says to consider potential leaching from the packaging.
In our experience, all but the largest packaging suppliers can’t provide information on potential trace impurities, leachables, migration from the packaging etc for cosmetics. However food contact materials have had to comply with their own regulations for a long time and we consider compliance with these regulations to be sufficient for cosmetics.
How can I keep the cost of my safety assessment(s) as low as possible?
The cost of a safety assessment report depends on a number of factors – the number and complexity of the individual ingredients for example. However, you can help to keep the costs down by:
-
Submitting your recipes on the company’s submission form (in Excel)
-
Putting all recipes in final percentages (and making sure it adds up to 100%)
-
Using correct INCI names
-
Placing all variants on the same worksheet as the base
Can I make cosmetic products that look like food?
Food Imitation – Products that could be confused with food:
The Regulations say that products which possess a form, odour, colour, appearance, packaging, labelling, volume or size, such that it is likely that consumers, especially children, will confuse them with foodstuffs, therefore endangering their health and safety, are prohibited.
Different competent authorities / Trading Standards may have differing opinions on how this is interpreted for actual products. If the cosmetic product is a colour and size that doesn’t look like foodstuff then it will be more acceptable. It is probably worth making some samples and checking with your local TS / competent authority.
What is an IFRA certificate?
An IFRA certificate is a document prepared by a fragrance compound manufacturer which lists the maximum amounts of a perfume that can be used in different product types. The safety assessor relies on the IFRA certificate to assure the safety of the perfume in the finished cosmetic product.
How can I calculate essential oil / parfum allergens for ingredient lists on labels?
There are 24 allergens which are currently ‘declarable’ in the EU and must be added to the ingredient lists.
Obtain the allergen list of the essential oil / perfume / aroma from the supplier.
Work out how much of each allergen is in the product, taking into account the percentage of that essential oil in the product by:
Amount of allergen in final product = Amount essential oil or perfume in product (%) x Amount of allergen in the fragrance (%)/100
If the product contains more than one essential oil / perfume / aroma, sum the individual allergens which are the same across different fragrances.
If the allergen is present in the final product above 0.01% for rinse-off products or above 0.001% for leave on products, then it needs to be listed on the label.
Do you assess products which contain cannabidiol / CBD?
It has recently been clarified that cannabidiol derived from extract or tincture or resin of cannabis is not allowed in cosmetic products, in accordance with the Single Convention (Narcotics, natural and synthetic: All substances listed in Tables I and II of the single Convention on narcotic drugs signed in New York on 30 March 1961) and I do not assess products containing CBD.
Will ‘Brexit’ have any effect on current or future cosmetic safety assessments?
The safety assessments prepared by GCS are valid in the EU and UK. Statutory Instrument (SI) issued by UK government regarding Cosmetic Regulations post-Brexit, show the same safety requirements as the EU and significant deviation is not expected, to allow continuing cross-border selling. Some divergences are now being seen – safety assessments at GCS will consider these on a case-by-case basis. If you have an RP based in the UK, CPSRs from GCS allow products to be sold across the UK (including Northern Ireland). If you have an RP based in an EU member state, CPSRs from GCS allow products to be sold across the EU (including Northern Ireland).
The location of the the safety assessor does not have to be in the EU, but EU authorities have advised safety assessors to ensure their UK-based qualifications can be shown to be equivalent to qualifications in an EU member state, and equivalence has been confirmed for qualifications obtained in the UK by the safety assessor at GCS.
Ready to reduce your cosmetic safety stress?
If you want an easier way of getting a high quality cosmetic safety assessment, you’re in the right spot. If you have your product recipe ready, click the button below to request your CPSR paperwork. But, if you have questions, use the button below to schedule a 20-minute chat and we’ll talk them through together.
Safety Assessor Qualifications
MSc (Distinction), University of Strathclyde
BSc (Hons) Chemistry, University of Nottingham
Certificate - Safety Assessment of Cosmetics in the EU, Vrije University Brussels
Get in Touch
If you would like to discuss any of your products or ranges, please fill out our contact form
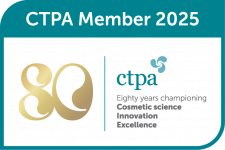
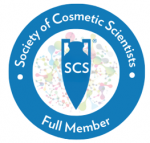
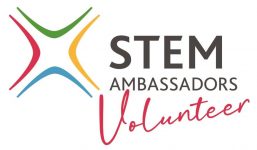
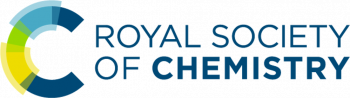